Entenda todos os detalhes referentes ao funcionamento, especificidades e manutenção do Motor Ciclo Diesel.
Neste artigo técnico, o foco é destacar os procedimentos de análise e diferenças em relação ao Ciclo Otto, ou seja, dos motores que funcionam com gasolina e etanol.
Inicialmente, vamos apresentar o princípio de funcionamento do Motor Ciclo Diesel e mais adiante fazer uma comparação com os motores Ciclo Otto.
Por fim, mostraremos de forma didática como realizar a manutenção preventiva. Um procedimento que tem como fim garantir seu perfeito funcionamento e aumento considerável da sua durabilidade.
Motor Ciclo Diesel: funcionamento
Sobre o funcionamento do motor a diesel, a característica construtiva principal é possuir alta taxa de compressão, começando com 16:1 a 24:1 ou até outros valores extremos.
Isso explica o aumento da temperatura do ar quando comprimido.
Em alguns casos o cabeçote de motores a Diesel tem sua face de baixo plana, sem câmara. Assim, todo o volume do cilindro é comprimida em milímetro, em um espaço pequeno que sobra quando o pistão chega em PMS.
Os motores do Ciclo Diesel ou motores de ignição por compressão utilizam o aumento da temperatura, devido a compressão de uma massa de ar, para dar início a reação de combustão. Nesse caso, somente ar é admitido.
Após a compressão, o combustível é pulverizado na massa de ar quente dando início a combustão.
Agora que você já sabe como funciona o motor a diesel, vamos partir para exemplos específicos e componentes.
Motor Ciclo Diesel 4 tempos
Os motores do Ciclo Diesel 4 tempos apresentam sistema de lubrificação, sendo o cárter o depósito de óleo lubrificante do motor.
Ele realiza o ciclo em quatro cursos, o que implica em duas voltas (720º) na árvore de manivelas. Os quatro cursos são os seguintes:
Primeiro curso: admissão
O pistão se desloca do PMS para o PMI.
Neste curso ocorre a admissão somente de ar no cilindro. Durante o processo, a válvula de admissão está aberta e a válvula de descarga está fechada.
O volume admitido é o volume de admissão ou cilindrada parcial do motor.
Nos motores Diesel o volume de ar aspirado é sempre o mesmo.
A variação da potência é obtida pela variação do volume de combustível injetado de acordo com a posição do acelerador.
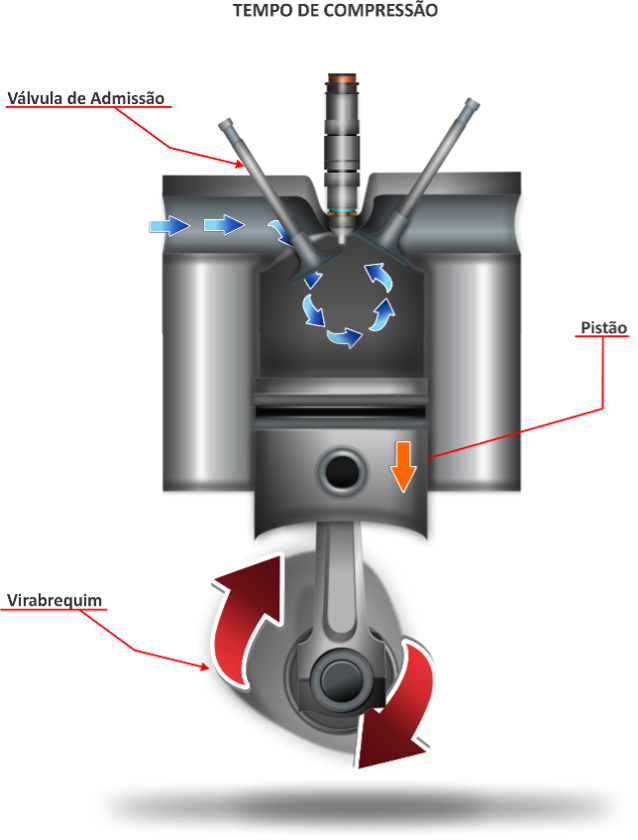
Segundo curso: compressão
O pistão se desloca do PMI para o PMS.
Neste curso ocorre a compressão do ar. As válvulas de admissão e descarga estão fechadas. A compressão do ar na câmara de combustão produz elevação da temperatura.
No fim da compressão para a relação volumétrica de 18:1, a pressão é de 40-45 kgf.cm² e a temperatura é de aproximadamente 800 ºC.
Da mesma maneira, o combustível é dosado e injetado na câmara de combustão.
A medida exata do combustível e o momento da injeção são fatores muito importantes para o bom funcionamento dos motores Diesel.
A injeção do combustível na câmara de combustão é feita pelo bico injetor. Imediatamente após a injeção, o combustível se inflama devido ao contato do combustível com o ar aquecido, iniciando-se a combustão.

Terceiro curso: expansão
O pistão se desloca do PMS para o PMI.
Neste curso ocorre a combustão da mistura ar/ combustível.
As válvulas de admissão e descarga estão fechadas. À medida que o processo de injeção está ocorrendo, o combustível vai se inflamando, aumentando a temperatura dos gases que tendem a se dilatar cada vez mais.
Durante a expansão, o pistão é acionado pela força de expansão dos gases, transformando a energia térmica em mecânica.
A força vinda da expansão dos gases é transmitida para a árvore de manivelas através da biela, promovendo assim, o movimento de rotação do motor. A expansão é o único curso que transforma energia.
Parte da energia transformada é armazenada na árvore de manivelas e no volante do motor, que será transmitida e consumida pelas rodas para movimentar o veículo.
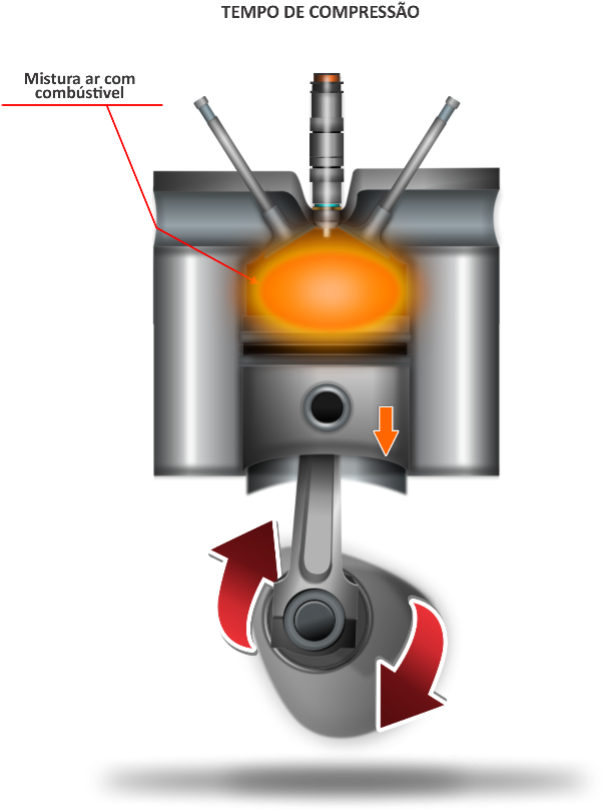
Quarto curso: descarga
O pistão se desloca do PMI para o PMS.
Neste curso ocorre a descarga dos resíduos da combustão.
A válvula de admissão está fechada e a de descarga está aberta. O movimento ascendente do pistão expulsa do cilindro os resíduos da combustão através da válvula de descarga.
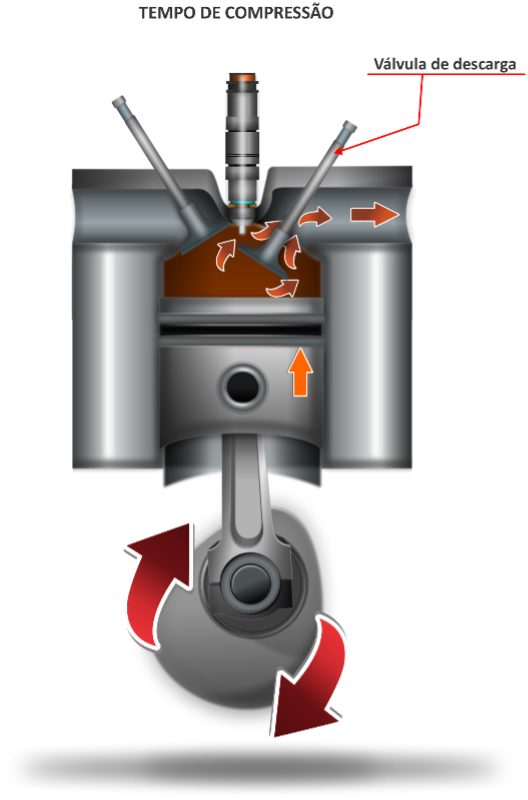
Principais componentes que constituem o Motor Diesel
Como podemos perceber na figura abaixo, os componentes de um Motor de Ciclo Diesel, são basicamente os mesmos que encontramos nos motores de Ciclo Otto.
Apenas alguns deles apresentam pequenas diferenças, as quais descreveremos mais à frente.
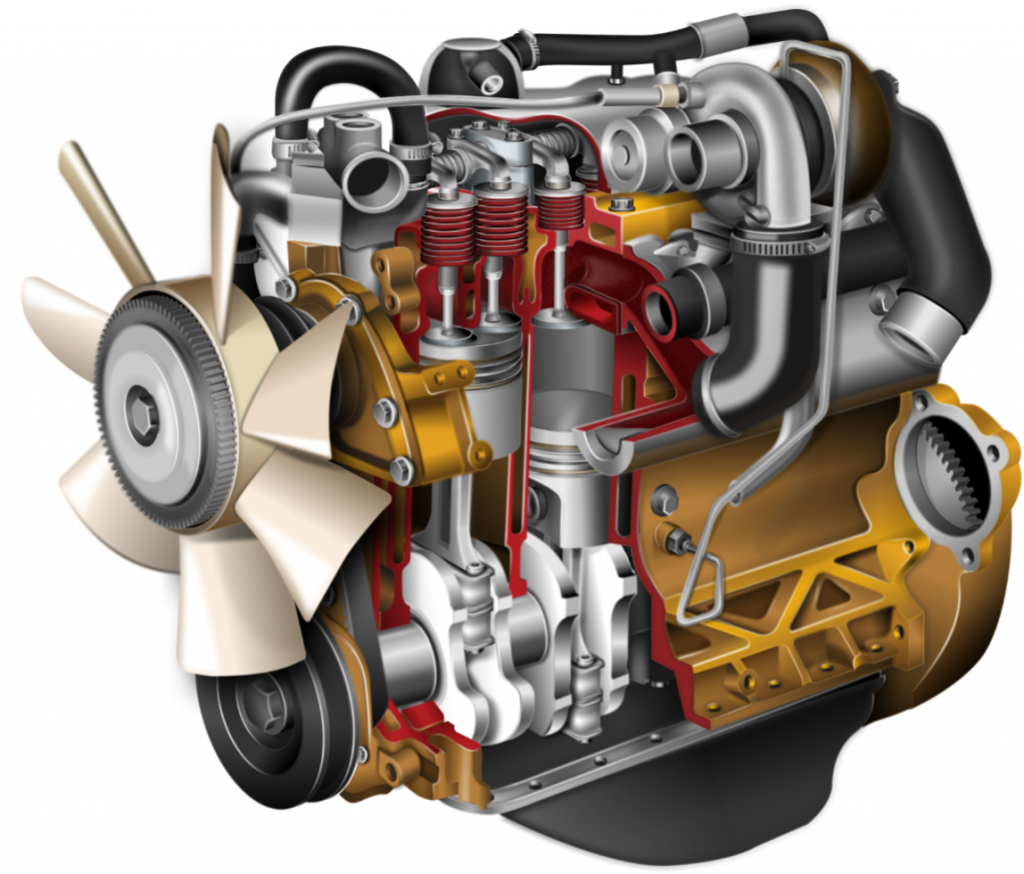
Confira a seguir os principais componentes do Motor Ciclo Diesel:
Bloco dos Cilindros
Os blocos dos cilindros são onde se alojam os conjuntos de cilindros, compostos pelos pistões com anéis de segmento, camisas, bielas, árvores de manivelas e de comando de válvulas, com seus mancais e buchas.
Geralmente é construído em ferro forjado cinza e usinado para receber a montagem dos componentes, com 4 cilindros arranjados em linha.
Normalmente é um bloco com saia profunda e 5 mancais de rolamento da árvore de manivelas.

Árvore de Manivelas
A árvore de manivelas é feita de liga de aço forjado. A barra e os munhões principais são endurecidos por indução para maior durabilidade.
Em várias aplicações temos uma engrenagem de acionamento do compensador de massa localizada na traseira da árvore de manivelas.
Geralmente nesse tipo de motor o anel do excitador do sensor de posição da árvore de manivelas está localizado entre a árvore de manivelas e a placa flexível/volante.
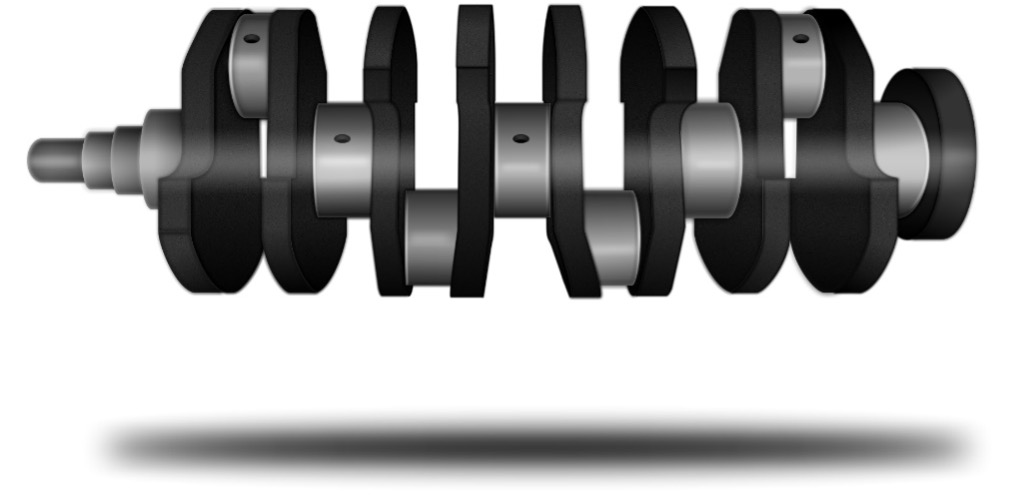
Biela e Pistão
As bielas são feitas de aço forjado e fraturadas. Os pinos do pistão são flutuantes.
Os pistões são feitos de liga de alumínio e possuem uma saia revestida com grafite.
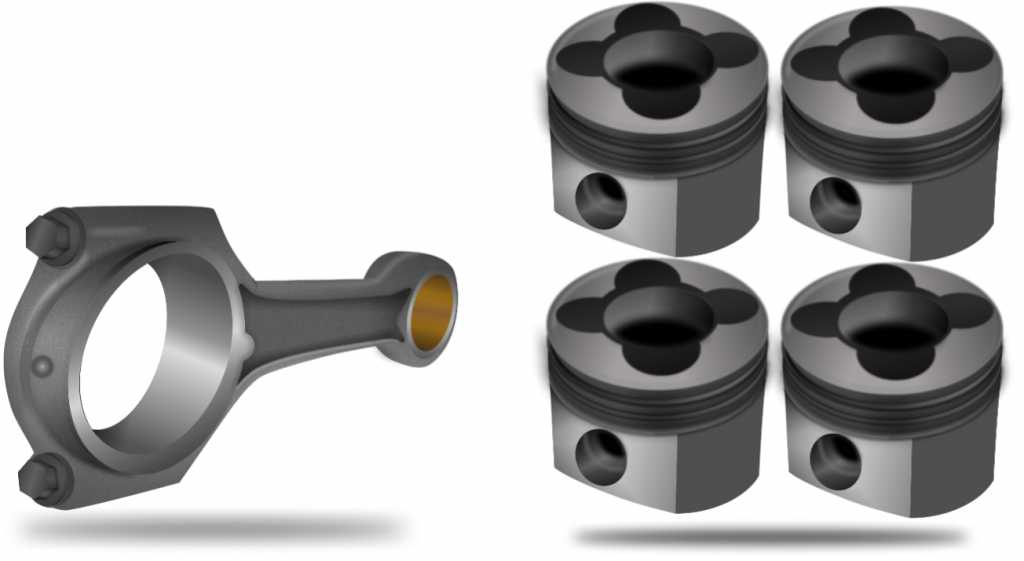
Cárter de óleo
O cárter é o reservatório do óleo lubrificante, utilizado pelo sistema de lubrificação.
É construído em ferro fundido, liga de alumínio fundido em matriz ou chapa de aço estampada.
Em alguns motores o cárter é do tipo estrutural, formando com o bloco uma estrutura rígida que funciona como chassis da máquina, como se vê em alguns tratores agrícolas.
O cárter de óleo inclui uma conexão à transmissão para proporcionar apoio estrutural extra.
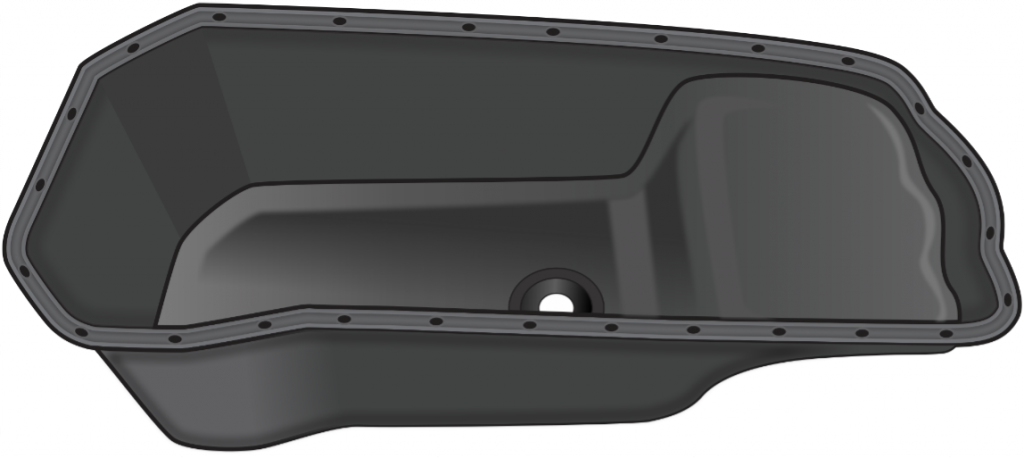
Conjunto do compensador de massa (Volante do motor)
O conjunto do compensador de massa é aparafusado na extremidade da árvore de manivelas. Sendo que, em alguns veículos possui ainda um sistema de amortecimento interno.
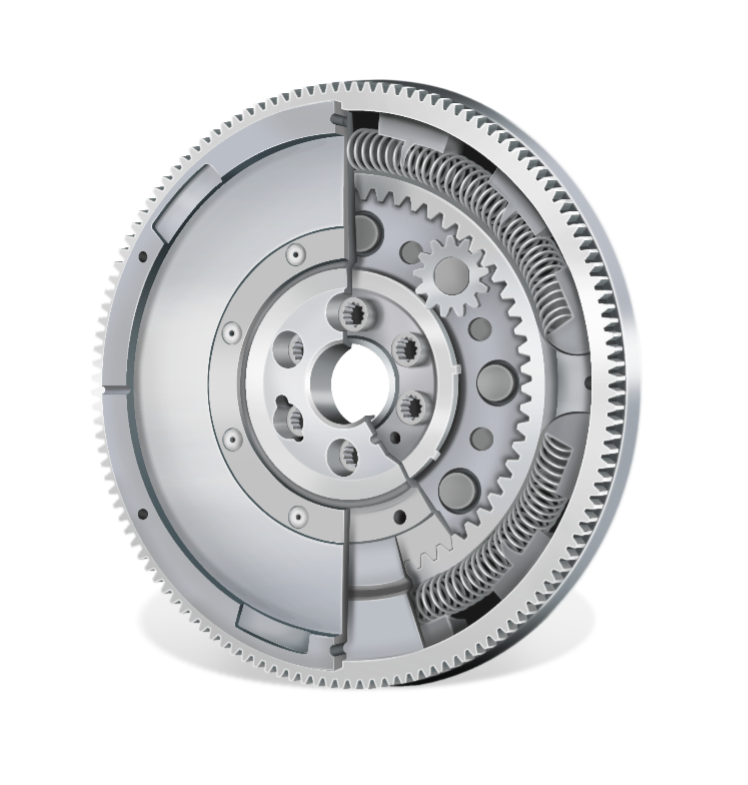
Válvulas
Em geral, existem duas válvulas de entrada e duas de saída em cada cilindro.
Os tuchos hidráulicos são usados em todas as válvulas. Nos motores atuais os tuchos são hidráulicos e estão localizados na parte inferior da mola da válvula para reduzir o atrito do movimento alternado do comando de válvulas.
Lacres da haste da válvula são utilizados em todas as válvulas.

Cabeçote
O cabeçote funciona, essencialmente, como “tampão” para os cilindros e acomoda os mecanismos das válvulas de admissão e escape, bicos injetores e canais de circulação do líquido de arrefecimento e lubrificação.
Dependendo do tipo de construção do motor, os cabeçotes podem ser individuais, quando existe um para cada cilindro, ou múltiplos, quando um mesmo cabeçote cobre mais de um cilindro.
Em algumas aplicações, o cabeçote do cilindro é feito de liga de alumínio. Os assentos e as guias da válvula feitos de metal em pó sinterizado são prensadas dentro do cabeçote do cilindro.
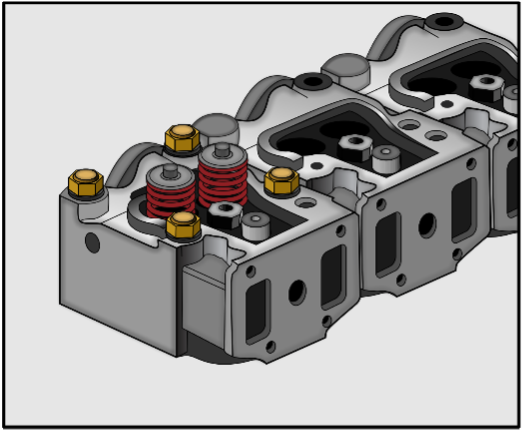
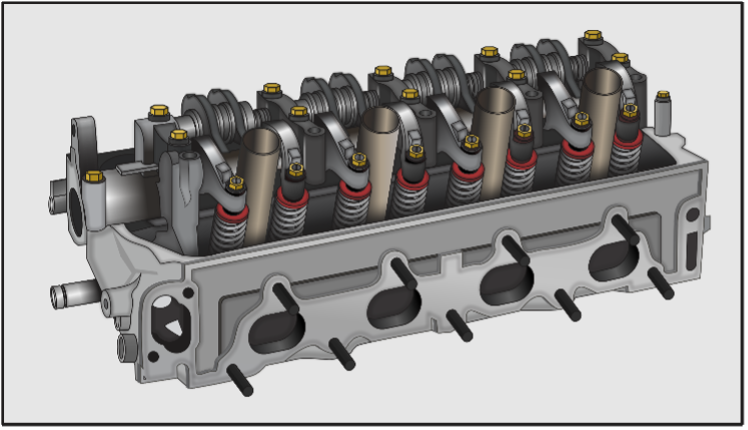
Comando de válvulas
Os comandos de válvulas, nas aplicações atuais, estão localizados no cabeçote e podem são acionados por correia ou corrente.
Na maioria das vezes, a correia ou corrente aciona a roda dentada no eixo-comando da admissão.
O eixo-comando da admissão aciona o eixo-comando da exaustão através de engrenagens prensadas sobre cada eixo-comando.

Balancins de válvulas
A grande maioria dos motores atuais, possuem balancins das válvulas roletados, que são ativados por tuchos hidráulicos, que reduzem o atrito e o ruído.

Qual a diferença entre Motor Ciclo Otto e Diesel?
A diferença entre motor ciclo Otto e Diesel é que em motores de ciclo Diesel, os projetos de arquitetura e estrutura são diferenciados devido a utilização constante em utilitários e veículos para carga pesada.
Diferente dos motores de ciclo Otto, onde predomina a aplicação em veículos de passeio.
Arquitetura
Os motores de ciclo Diesel são na maioria das vezes, em linha. Motores em “V” movidos a Diesel são geralmente utilizados em veículos de passeio ou veículos esportivos.
O pouco uso dos motores em “V” nos caminhões, deve-se ao fato de que o comprimento dos motores de quatro cilindros ou seis cilindros em linha não interfere no design e na aerodinâmica. Isto diminui o custo de desenvolvimento.
Estrutura
A estrutura de um motor de ciclo Diesel é reforçada, se compararmos com um motor ciclo Otto.
Estes reforços ajudam na diminuição das vibrações, aumento da durabilidade e geralmente são encontrados nos pontos de fixação do motor ou de agregados.
Diferença entre componentes móveis
Pistão Ciclo Otto
Os pistões dos motores ciclo Otto possuem a superfície da câmara de combustão plana ou apenas com pequenas cavidades. Estas cavidades são espaços para a abertura das válvulas.
É importante estar atento à tabela de regulagem de válvulas motor diesel para que tudo esteja funcionando corretamente.

Pistão Ciclo Diesel
Nos motores Diesel são empregadas câmaras de combustão no próprio pistão. Estas cavidades auxiliam na distribuição da energia gerada pelo processo de combustão.
Geralmente possuem no centro, um ressalto que, no momento de compressão, gera um turbilhonamento do ar, que facilita a mistura com o Diesel.
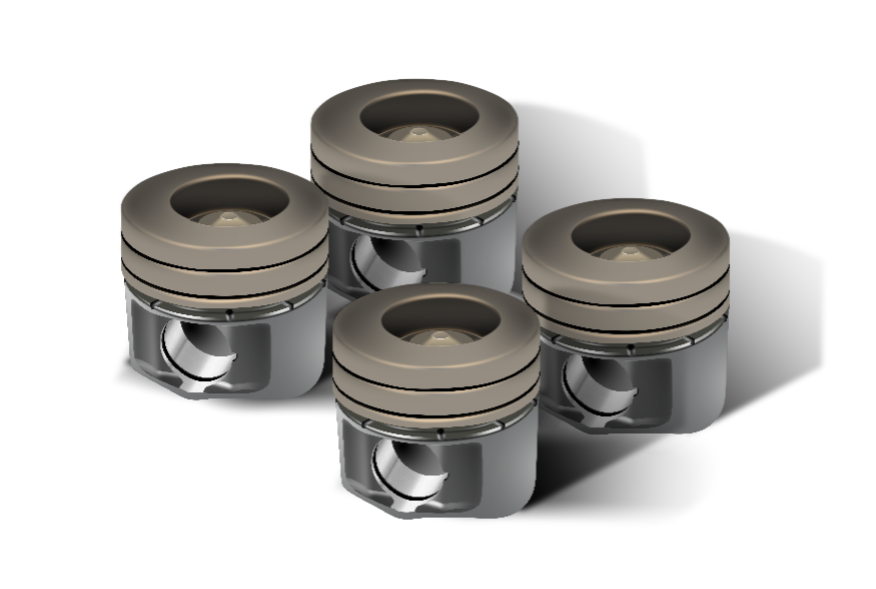
Os sistemas do Motor Diesel
As diferenças básicas entre os diversos tipos de motores Diesel residem, essencialmente, sobre os sistemas que os compõem.
Todos funcionam seguindo as mesmas leis da termodinâmica, porém as alterações de projeto que se efetuam sobre os sistemas e seus componentes resultam em características de operação que os tornam adequados para aplicações diferentes.
Dessa maneira, a tecnologia de motores ciclo diesel avançam com o tempo e assim, criam-se componentes novos com a finalidade de otimizar o sistema.
Os sistemas que constituem os motores Diesel são:
- Sistema de admissão de ar motor diesel;
- Sistema de alimentação de combustível;
- Sistema de vela aquecedora;
- Sistema de lubrificação;
- Sistema de arrefecimento;
- Sistema de escape;
Sistema de admissão de ar motor diesel
O sistema de ar é planejado para suprir o motor de ar limpo (oxigênio) e em quantidade que garanta o melhor rendimento do combustível durante seu funcionamento.
O circuito envolve a admissão do ar, filtragem, participação na combustão e exaustão para o meio exterior.
O ar aspirado pelo motor deverá passar obrigatoriamente por um filtro de ar de boa qualidade, pois ele é responsável pela retenção das partículas contidas no ar ambiente.
Existem três tipos de sistema que são os mais usuais em motores Diesel:
- Sistema de aspiração natural
- Sistema turbo-alimentado
- Sistema turbo-alimentado com pós-arrefecimento
1) Sistema de aspiração natural
No sistema de aspiração natural, o ar é admitido para dentro do cilindro pela diferença de pressão atmosférica, provocada pela sucção decorrente do movimento descendente dos pistões. Passa pela filtragem, caminha através do coletor de admissão e alcança a câmara de combustão.
Após a combustão, os gases resultantes da queima são empurrados pelos pistões por meio do coletor de escape para o meio exterior.
2) Sistema turbo-alimentado
O turbo compressor, conhecido popularmente como turbo, é basicamente uma bomba de ar. O turbo compressor tem a função de comprimir, fazendo caber mais massa de ar dentro do mesmo volume das câmaras de combustão.
Isso, consequentemente, favorece a combustão de mais combustível, gerando mais potência e torque no motor.
Os gases quentes de escape que deixam o motor após a combustão fazem girar o rotor da turbina. Este rotor é ligado a um outro rotor por um eixo.
A rotação do rotor da turbina provoca a rotação, na mesma velocidade, do rotor do compressor. A rotação do rotor do compressor puxa o ar da atmosfera, o comprime e o bombeia para dentro do motor.
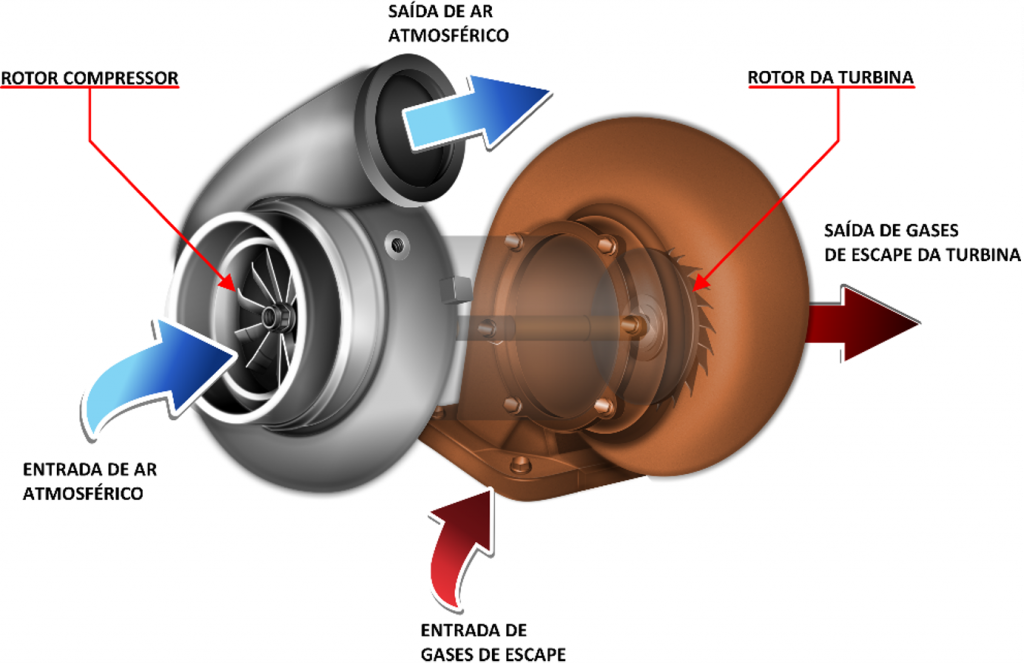
Característica do turbo-alimentador
O turbo-alimentador possibilita que um motor pequeno tenha a mesma potência que um motor muito maior.
Além disso, torna motores maiores ainda mais potentes, auxiliando na redução da emissão de gases poluentes, pois o turbo injeta mais ar ao motor fazendo com que a combustão seja mais completa e mais limpa. Com isso, diminui o consumo de combustível.
A perda de calor pelo atrito aumenta drasticamente com o aumento do tamanho do motor.
Por serem menores, os motores turbo-alimentados aproveitam melhor a energia, desperdiçando menos energia por calor e atrito.
Outro ponto importante é que ele previne a perda de potência e a queima incompleta em grandes altitudes – fumaça preta.
Turbo de Geometria Variável
O turbo TGV (Geometria Variável) diferencia-se do turbo convencional pela utilização de um prato ou coroa, no qual estão montadas umas aletas móveis.
Elas podem ser orientadas – todas em conjunto – num ângulo determinado, mediante um mecanismo de vareta e alavanca empurradas por uma cápsula pneumática.
Para conseguir a máxima compressão do ar em baixas rotações deve-se fechar as aletas.
Já que diminuindo a secção entre elas, aumenta a velocidade dos gases de escape que incidem com mais força sobre as pás do rodete da turbina (menor Secção = maior velocidade).
Quando o motor aumenta sua rotação e, consequentemente, aumenta a pressão no coletor de admissão, a cápsula pneumática detecta-o através de um tubo ligado diretamente ao coletor de admissão.
Transforma-o num movimento que empurra o sistema de comando das aletas, para que estas se movam para uma posição de abertura. Isso faz diminuir a velocidade dos gases de escape que incidem sobre a turbina (maior secção = menor velocidade).
As aletas estão montadas sobre uma coroa, é possível regular o veio roscado de união à cápsula pneumática para que as aletas abram antes ou depois.
Se as aletas estiverem em abertura máxima, indica que há uma avaria, já que a máxima inclinação só é adotada para a função de emergência.
As vantagens do turbo-compressor (TGV) advêm de conseguir um funcionamento mais progressivo do motor sobrealimentado.
A diferença dos primeiros motores dotados com turbo-compressor convencional, onde havia um grande salto de potência de baixas rotações para altas, o comportamento deixou de ser brusco para conseguir uma curva de potência muito progressiva com grande quantidade de ar. Desde baixas rotações e mantido durante uma ampla zona do nº de rotações do motor.
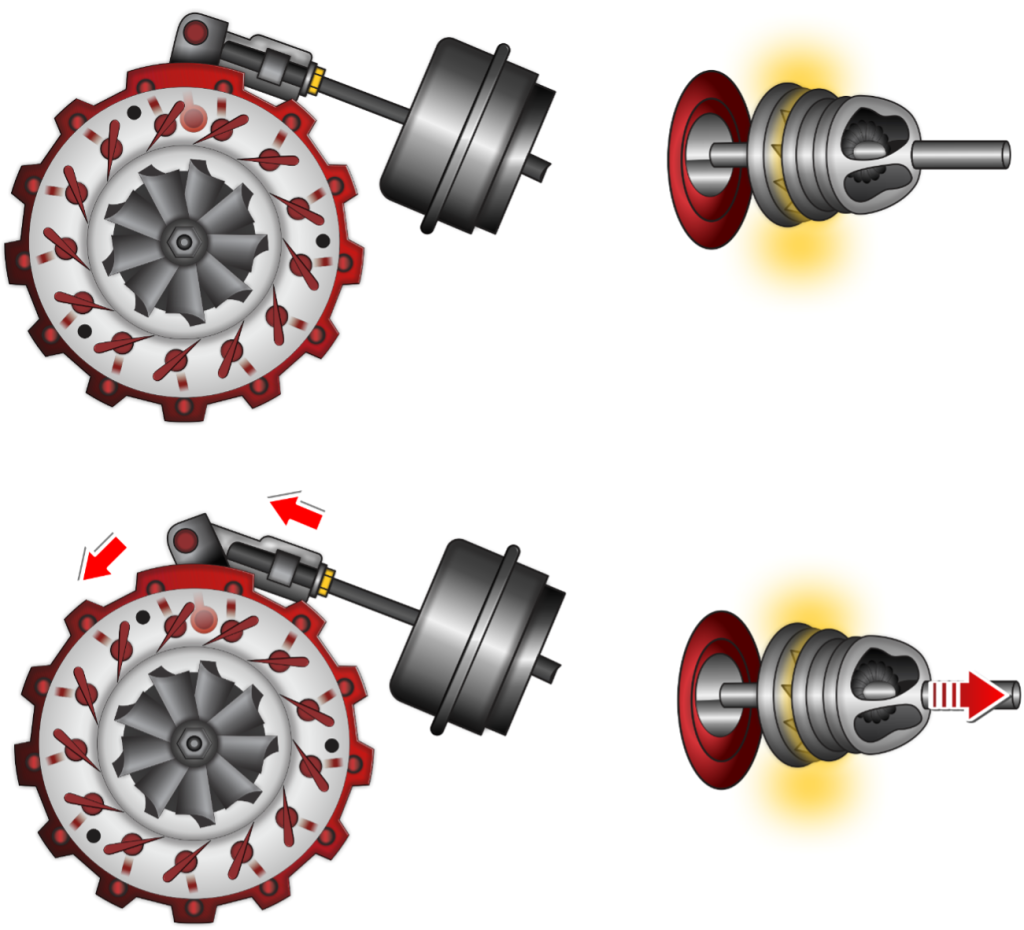
3) Sistema turbo-alimentado com pós-arrefecimento
O Sistema Intercooler – Pós-resfriado ou sistema turbo-alimentado com pós-arrefecimento funciona da seguinte maneira: o ar comprimido sai da carcaça do compressor muito quente, por causa dos efeitos do turbo compressor e do atrito. O calor provoca a expansão dos fluídos diminuindo a sua densidade.
Então, torna-se necessário fazer com que o ar se resfrie de alguma maneira antes de ser recebido pelas câmaras de combustão do motor. Isto é o que faz o Intercooler.
Ele reduz a temperatura do ar admitido fazendo com que ele fique ainda mais denso quando entra na câmara. O Intercooler também ajuda a manter a temperatura baixa dentro da câmara de combustão.
O Intercooler localiza-se no circuito de ar entre o turbo e cilindro do motor. Um compressor convencional pode girar a uma rotação de 100.000 rpm ou mais. Por isso, alguns cuidados de lubrificação e operação são necessários.
Muitas das falhas nos turbos são causadas pela deficiência de lubrificação como atraso na lubrificação, restrição ou falta do fluxo de óleo, entrada de impurezas no óleo ou impurezas pelo rotor da turbina ou do compressor.
Esquema Genérico
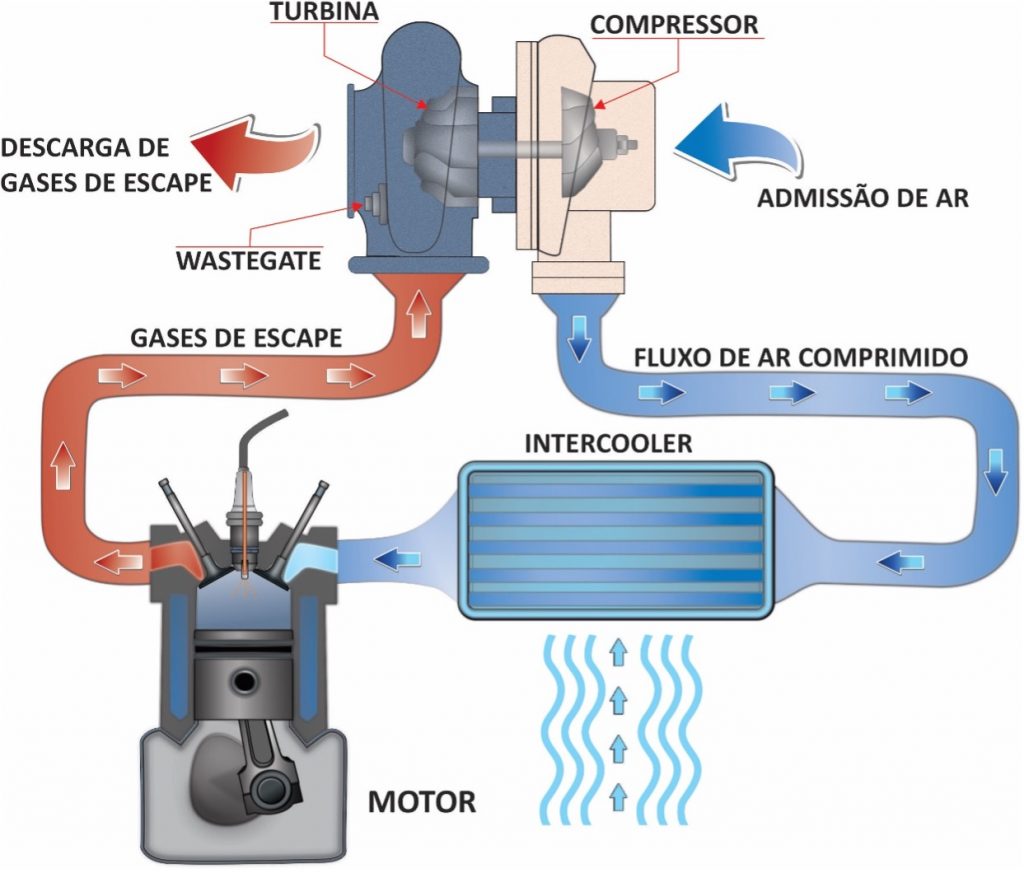
O turbo compressor aumenta a energia do motor bombeando ar para as câmaras de combustão, permitindo que uma maior quantidade de combustível entre em combustão na razão ótima entre ar e combustível.
Ele possui alguns componentes auxiliares, como:
Sensor de pressão do turbo compressor
O sensor de pressão do turbo é montado no coletor de admissão e mede a pressão de explosão e a temperatura do ar.
Sistema de Alimentação de Combustível
O Sistema de Alimentação de Combustível do motor que equipa os veículos atuais é composto dos seguintes componentes:
- Tanque de Combustível;
- Bomba de Combustível;
- Linha de Combustível;
- Filtro de Combustível;
- Bomba de Alta Pressão;
- Regulador de Pressão;
- Common Rail;
- Sensor de Pressão;
- Linha de Alta Pressão;
- Injetores;
- Linha de Retorno;
- Reservatório de Retorno de combustível.
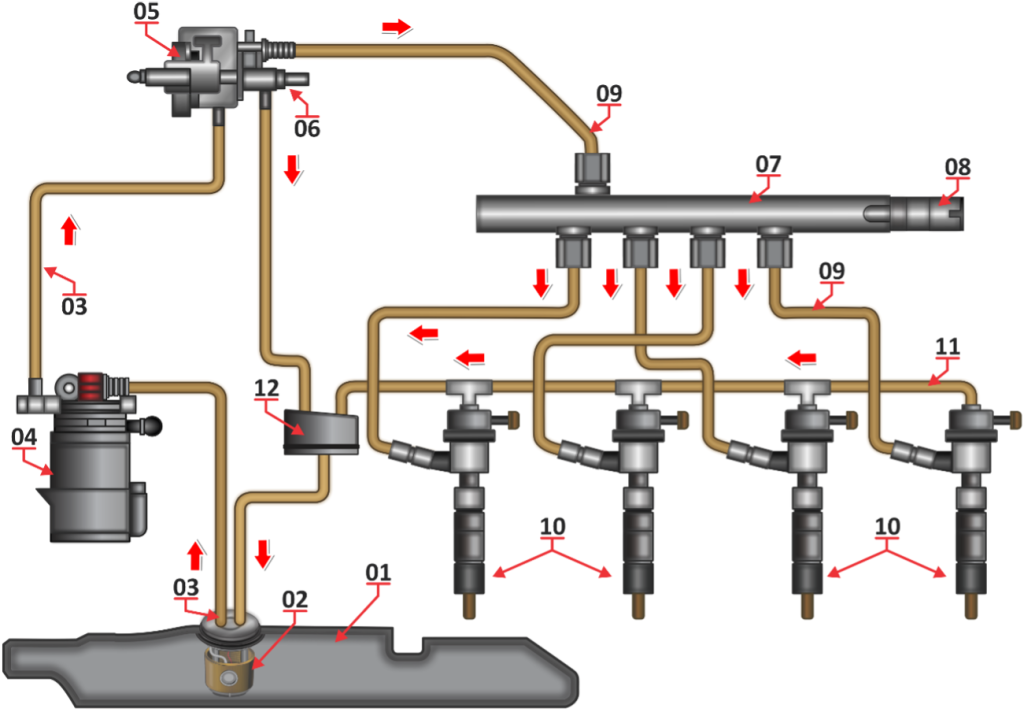
Tanque de combustível
O tanque de combustível armazena o suprimento do veículo. É mantido em posição por 2 cintas metálicas presas no chassi e é feito com polietileno de alta densidade.
A tampa do enchedor de combustível tem um dispositivo de limitação de torque que evita que a tampa seja muito apertada.
Para instalar, gire a tampa no sentido horário até você ouvir um clique. Isto indica que a tampa está completamente assentada.
Bomba de combustível
O módulo do controle da bomba de combustível fica localizado dentro do tanque de combustível e fornece combustível em baixa pressão para a bomba de alta pressão.
O módulo de controle do motor (ECM) controla a operação da bomba de combustível de baixa pressão. É formado pelos seguintes componentes principais:
- Sensor de nível do combustível: boia, pescador e resistor de cerâmica. A posição do pescador indica o nível do combustível. O sensor de nível contém um resistor variável que muda sua resistência de acordo com a quantidade de combustível no tanque. O ECM também monitora os dados de nível de combustível para diversos diagnósticos.
- Bomba de combustível e o conjunto do reservatório: instalada no reservatório, consiste em um modelo elétrico. O combustível é bombeado para a bomba de injeção de combustível mecânica na pressão e no fluxo especificados. O módulo de controle controla a operação da bomba elétrica através de um relé.
- Peneira de filtração: instalada no lado inferior do envio de combustível. É feita de malha plástica. As funções da peneira são filtrar os contaminantes e drenar o combustível.
Conjunto do filtro de combustível
O combustível é enviado por meio das linhas de combustível traseiras para o conjunto do filtro de combustível.
Esse módulo possui o elemento de filtragem de papel, que coleta partículas do combustível que podem danificar o sistema de injeção de combustível.
O separador de água do combustível possui um elemento de papel do filtro que retém partículas do combustível que podem danificar o sistema de injeção.
É projetado para permitir que partículas de água retidas assentem no fundo do conjunto do filtro.
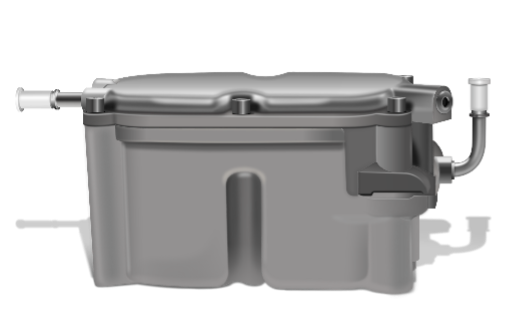
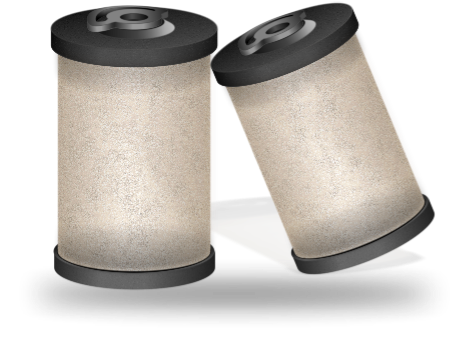
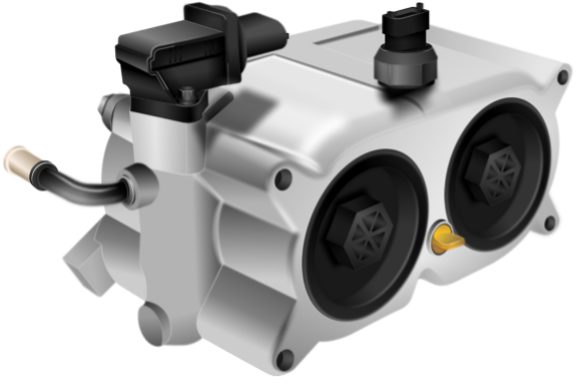
Aquecedor de combustível
O aquecedor de combustível, localizado no módulo de condicionamento de combustível, é controlado pelo módulo de controle do motor (ECM).
Quando a temperatura do combustível está abaixo do nível calibrado o ECM dá o comando para o relê do aquecedor LIGAR.
Com o relê LIGADO a tensão da bateria é fornecida para o aquecedor de combustível para ajudar na operação em clima frio.
Sensor de água no combustível
O sensor de água no combustível é um sensor de 3 fios que monitora a presença de Diesel e água.
Quando existe água, o ECM detecta uma baixa voltagem no circuito de sinal e envia uma mensagem de dados seriais para o painel de instrumentos para exibir a mensagem: “Água no combustível necessário manutenção.”
Tubo de retorno e alimentação de combustível
O tubo de alimentação serve para conduzir o combustível do tanque até o compartimento do filtro/aquecimento do combustível.
O cano de retorno leva o combustível dos conjuntos de volta para o tanque.
Bomba de injeção de combustível de alta pressão
A bomba de injeção é uma bomba mecânica de alta pressão. O combustível é bombeado para o duto de injeção de combustível – Common Rail – em uma pressão especificada.
A pressão do combustível é regulada pelo regulador de pressão que fica localizado no lado de admissão da bomba de alta pressão, controlada pelo módulo de controle do motor (ECM).
O excesso de combustível da bomba de alta pressão de combustível retorna para o tanque de combustível através do cano de retorno.
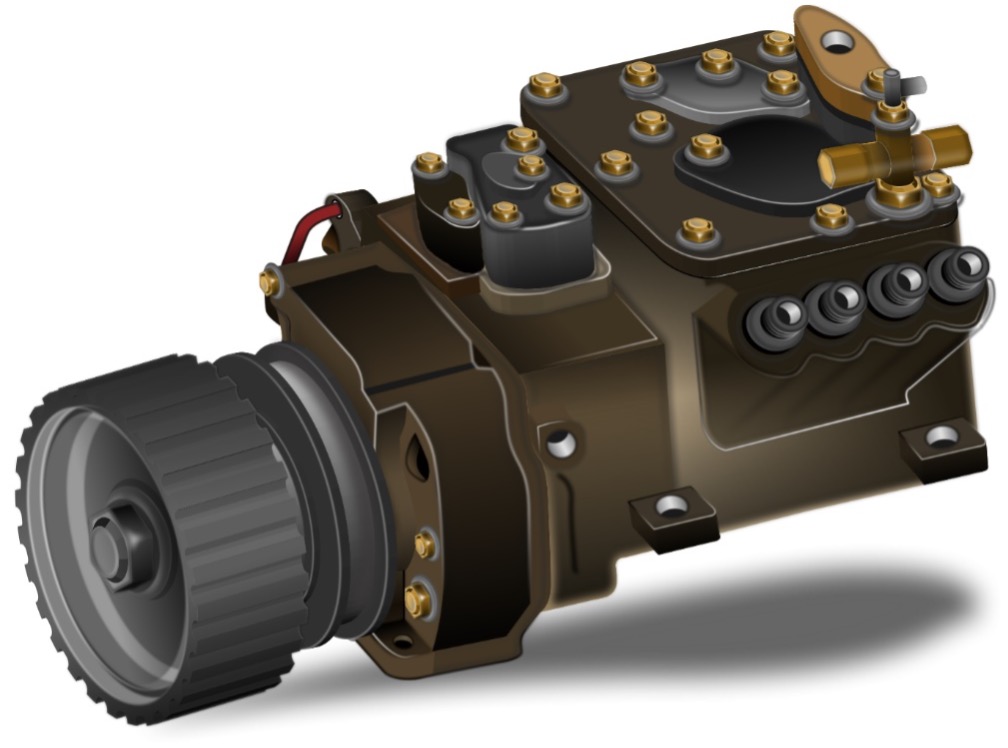
Regulador de pressão do combustível
O módulo de controle do motor (ECM) controla a pressão do Common Rail usando um regulador de pressão modulado por uma largura de pulso.
O regulador de pressão do combustível fica localizado na entrada da bomba de alta pressão e mede a quantidade de combustível que entra na bomba.
O ECM varia a tensão modulada da largura de pulso para o regulador de pressão do combustível para controlar a pressão do Common Rail.
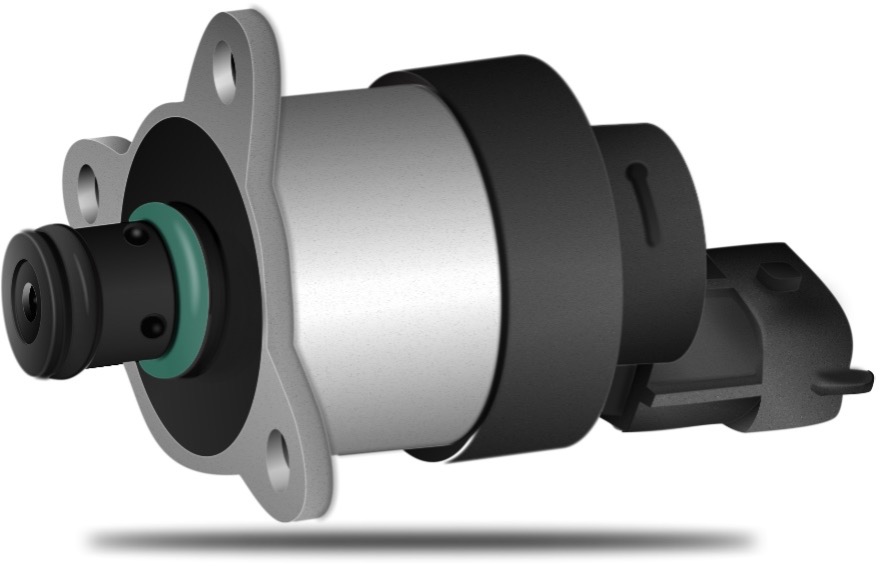
Sensor da pressão do combustível
O sensor de pressão do combustível fica localizado na frente do conjunto Common Rail. Esse sensor de pressão fornece ao módulo de controle do motor (ECM) uma indicação da pressão real do duto.
O ECM usa esta informação para regular a pressão do combustível, comandando o regulador de pressão para obter a pressão desejada.
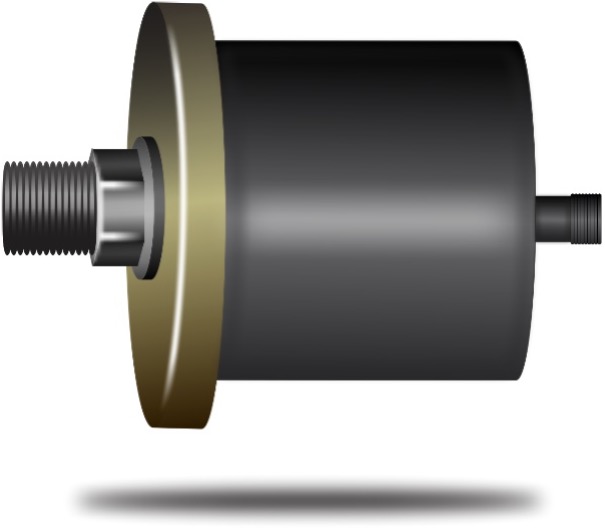
Conjunto distribuidor de combustível (Common Rail)
Desde a construção do primeiro motor Diesel, o principal problema era o processo de injeção do combustível para a combustão ideal. Os sistemas existentes não sofreram grandes modificações no decorrer dos anos.
As principais alterações, que resultaram em evolução significativa, foram, primeiramente o advento da bomba rotativa em linha, desenvolvida por Robert Bosch em 1927, que permitiu aos motores alcançarem rotações mais elevadas e, consequentemente, mais potência.
Em 1997, surge um motor Diesel dotado de um sistema de injeção revolucionário, que se denominou de JTD. Tal sistema, aumentava a potência e o torque com redução do consumo e, por consequência, os níveis de emissões.
Esse sistema foi evoluindo até que em 2003 chegam ao mercado os novos motores equipados com um sistema, que ganhou a denominação de COMMON RAIL.
O Common Rail, fica acoplado ao cabeçote dos cilindros, distribuindo o combustível pressurizado para os injetores de combustível através das linhas de combustível.
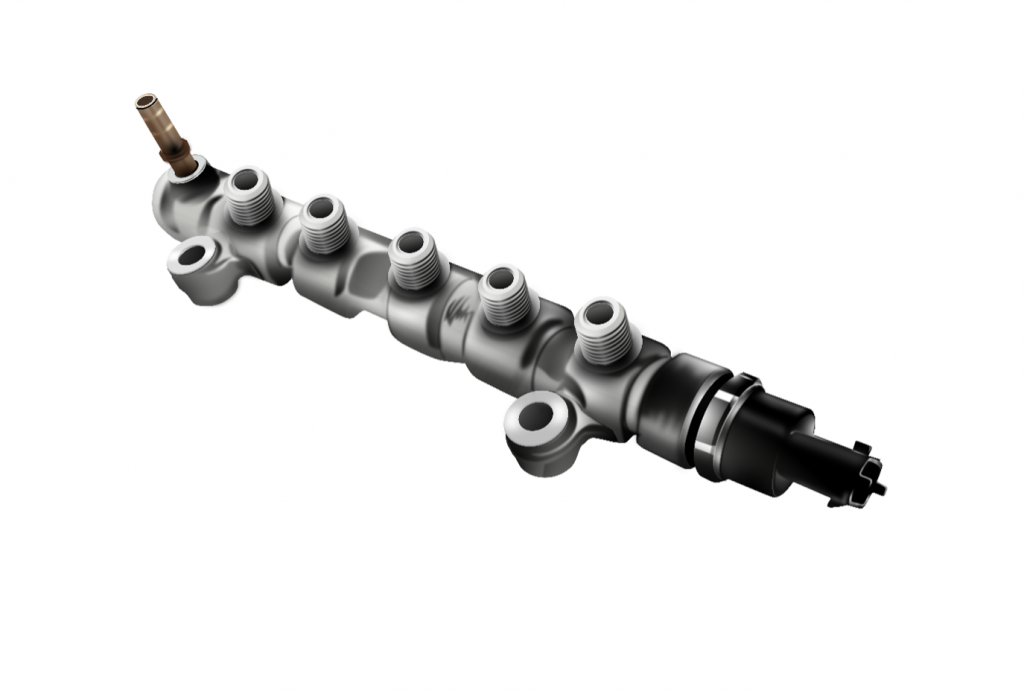
Injetores de combustível
Os injetores de combustível estão localizados acima de cada cilindro e fornecem combustível diretamente para dentro do cilindro.
Cada injetor possui um tubo de combustível de alta pressão que vem do duto e uma linha de retorno. O módulo de controle do motor (ECM) aciona os solenoides que liberam a injeção de combustível.
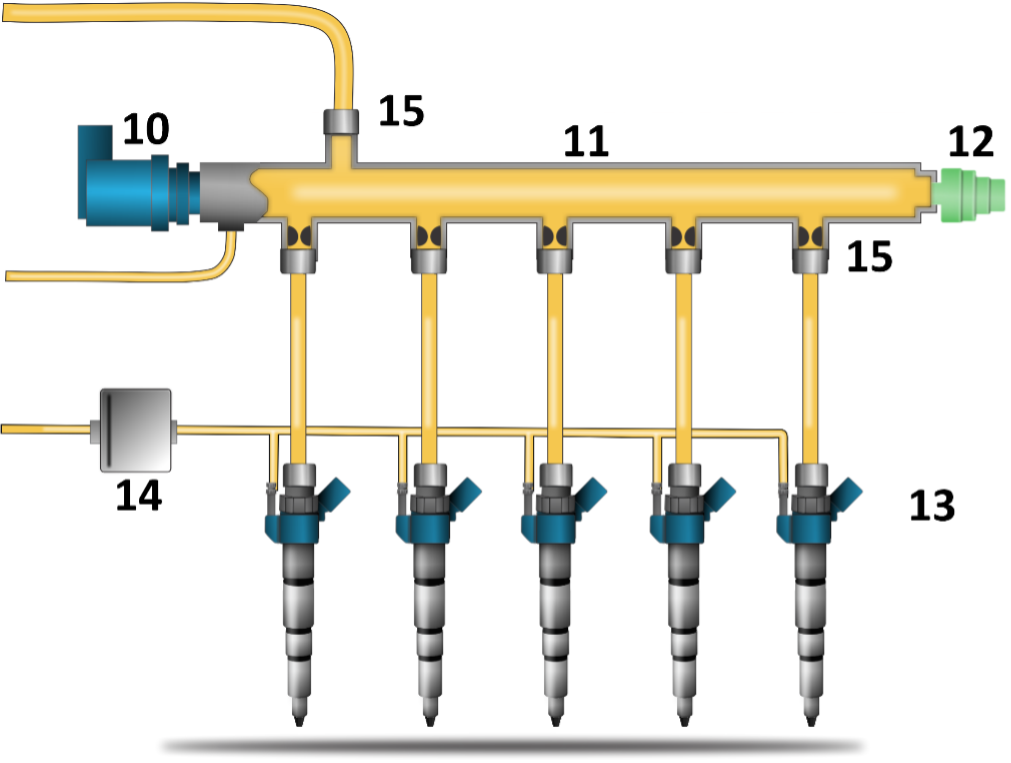
Os injetores possuem códigos impressos nos solenoides – topo do injetor – que são utilizados quando a unidade de comando tem uma função de software chamada IQA, Injection Quantity Adjustment – Quantidade de ajuste da injeção.
Na produção do injetor existe um desvio, como em qualquer produção, fazendo com que os injetores não tenham exatamente a mesma quantidade injetada.
É realizada uma triagem nos lotes dos injetores, mapeando qual é o desvio de injeção que os injetores possuem.
Este código pode indicar que o injetor desvia por exemplo + 5 mm³, um outro desvia – 2mm³, do valor médio. Desta forma, a unidade de comando lê o código e faz o ajuste no tempo em que o injetor fica aberto, aumentando ou reduzindo esse tempo.
Isto é feito para que todos os injetores tenham a mesma quantidade. Uma vez que o mapa de injeção é feito com um jogo de injetores médios em bancada, onde em determinado ponto de rotação e pressão, para atingir uma quantidade de injeção, o injetor tem que ficar X microssegundos aberto.
Estes valores alimentam um mapa na unidade de comando e depois são aplicados em motor para considerar, por exemplo, a contra pressão de combustão e a temperatura de combustível, que acaba influenciando neste tempo de injeção também. Isto é muito importante quando os níveis de emissões são muito apertados para serem atingidos (EURO IV, V…).
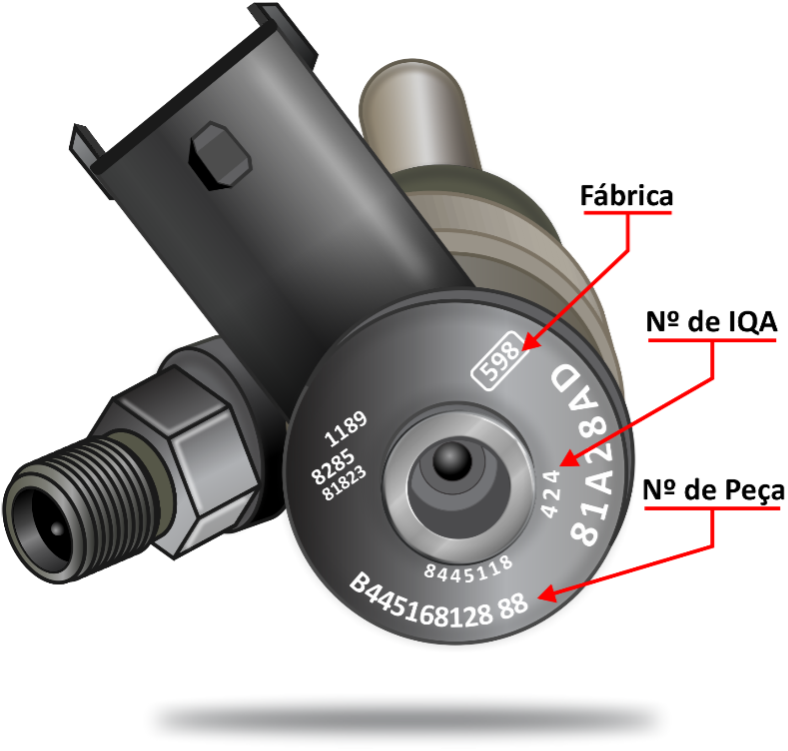
Em caso de substituição, o bico injetor deve ser adaptado à Unidade de Controle do motor por meio do scanner automotivo.
A calibração da injeção deve ser realizada com o objetivo de:
- Reduzir o consumo de combustível;
- Reduzir as emissões dos gases de escapamento;
- Produzir um funcionamento mais suave do motor.
Sistema de Escapamento
O sistema de escapamento leva os gases, tratados pelo conjunto conversor catalítico e filtro de partículas, para o silencioso, que diminui o ruído do escapamento e os libera na atmosfera.
Motores a Diesel têm como crítica a emissão dos óxidos nitrogenados, NOx (NO + NO2) e de material particulado.
Os modernos motores ciclo Diesel, são equipados com catalisador de oxidação do Diesel (DOC) e filtro de partículas, conhecido pela sigla DPF.
O DPF (filtro de particulados Diesel) coleta materiais particulados para minimizar a descarga de fuligem para a atmosfera. A captura dos particulados pelo DPF é capaz de reduzir a PM (quantidade de particulados) em mais de 90%.
Os gases fluem através de canais e as partículas de fuligem são retidas nas paredes. Esse componente é monitorado pelo ECM e quando atinge certo nível de saturação, requer um processo de limpeza, conhecido como regeneração.
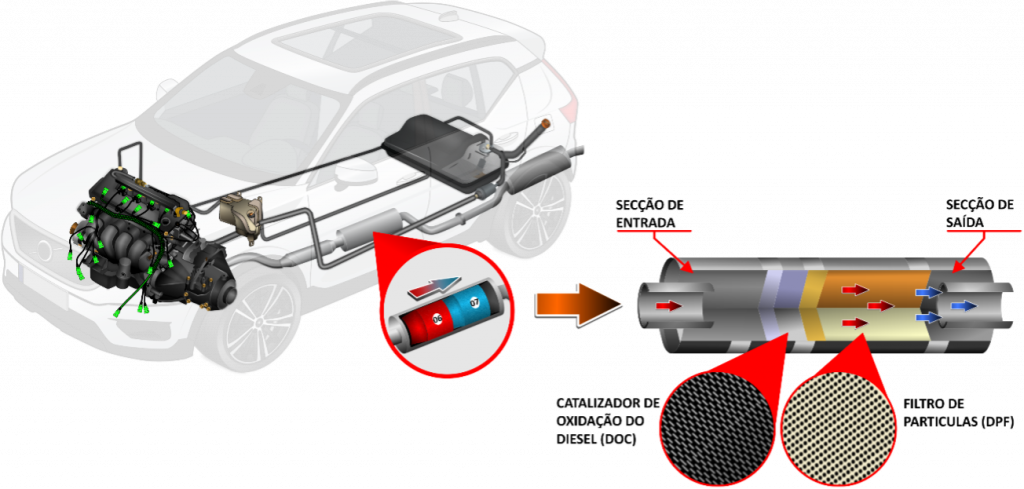
Sistema EGR
Os sistemas EGR têm sido usados em veículos há muitos anos. O principal objetivo desse sistema é controlar a temperatura da câmara de combustão. Isto é feito através da redução da quantidade de Óxidos de Nitrogênio (NOx) no escapamento.
Normalmente, o motor admite o ar através do corpo de borboleta, que o direciona para o coletor de admissão.
A válvula EGR é colocada numa posição tal que, quando ela é aberta, um pouco dos gases de escapamento flui também para a admissão.
Embora o volume de gases na câmara de combustão seja o mesmo, haverá menos ar para queimar quando o combustível é inflamado, de modo que a temperatura e a pressão do cilindro diminuirão.
Menos oxigênio e temperaturas mais baixas equivalem a uma queda nos níveis de emissão de NOx.
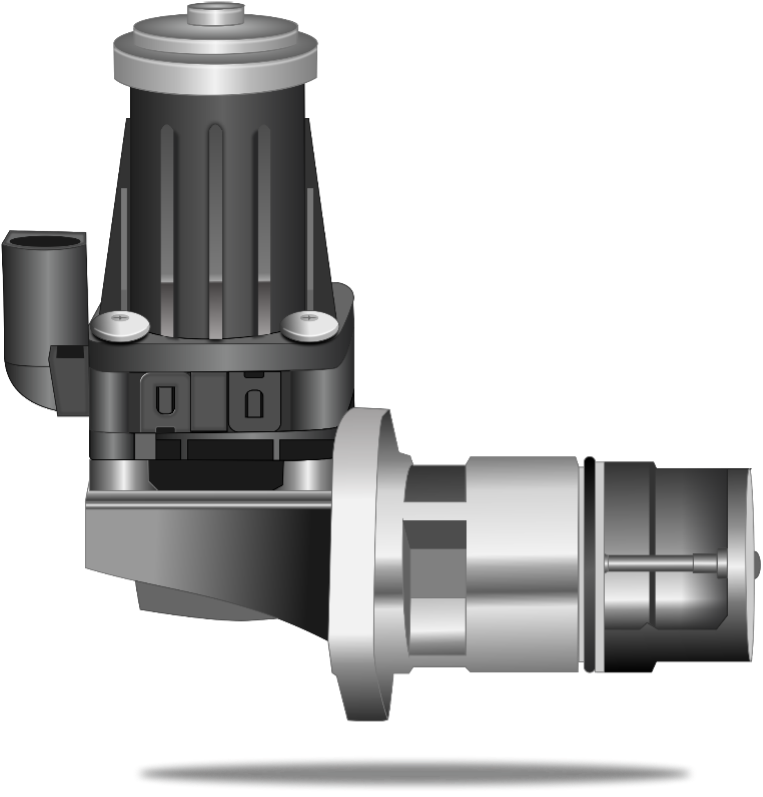
Descrição do sistema de recirculação dos gases de escapamento (EGR)
O sistema EGR é usado para reduzir os níveis de emissão de óxidos de nitrogênio (NOx) causados pelas altas temperaturas de combustão. Em temperaturas acima de 1371 ºC, o oxigênio e o nitrogênio se combinam para formar NOx.
Introduzir pequenas quantidades de gás do escapamento na câmara de combustão desloca a quantidade de oxigênio que entra no motor.
Com menos oxigênio na mistura de ar/combustível, as pressões da combustão são reduzidas, e como resultado, as temperaturas de combustão são diminuídas, restringindo a formação de NOX.
Operação do sistema de recirculação dos gases do escapamento (EGR)
O ar que entra pelo compartimento do filtro de ar de admissão é comprimido pelo turbo compressor, resfriado pelo intercooler e misturado com o gás de escape resfriado, que vem da válvula de recirculação do gás de escape EGR.
O gás de escape se mistura com o ar de admissão para satisfazer as emissões, o desempenho, a economia de combustível e o resfriamento do processo de combustão.
O sinal do sensor de fluxo da massa de ar (MAF) é usado pelo ECM para detectar a quantidade adequada de fluxo do EGR.
O ECM fechará a válvula EGR, e então a abrirá até 100%. Então o ECM calculará a diferença do MAF para determinar se o fluxo adequado do EGR foi detectado.
O sistema EGR também evita a formação de gases relacionados aos NOx, que são uma causa comum para reprovação dos testes de emissões.
Quando ocorre uma falha no sistema EGR, o sistema de admissão de ar e o sistema de escape devem ser inspecionados a fim de isolar a causa raiz.
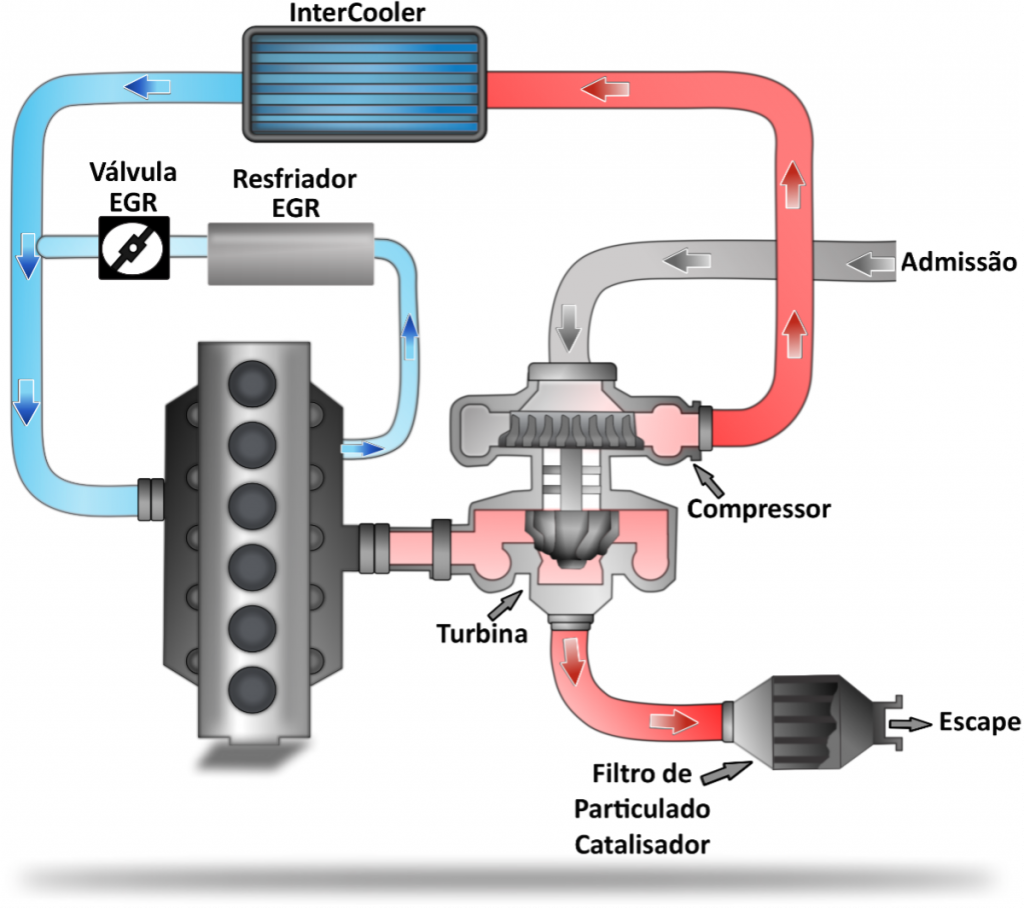
Manutenção preventiva nos motores Diesel
Confira os serviços de manutenção que devem ser executados diariamente:
- Verifique o nível de óleo do Carter através da vareta de nível, se necessário, abasteça-o através do bocal com óleo recomendado. O nível de óleo deve ser mantido entre as marcações máxima e mínima. Nunca opere o motor com o nível fora desses limites.
- Observe o nível d’água. Quando necessário, abasteça o radiador com água limpa e tratada.
- Faça uma inspeção visual no motor em busca de vazamentos d’água, óleos lubrificantes, combustível e gases de escape; entrada de impurezas na admissão, braçadeiras e parafusos frouxos ou quaisquer avarias e ruídos anormais.
- Verifique também o estado e a tensão das correias. Se necessário, faça o ajuste conforme recomendado no Manual de Operação e Manutenção, fique atento à tabela de aperto de motores diesel.
Serviços de manutenção que devem ser executados semanalmente:
- Os períodos de limpeza ou troca dos elementos do filtro de ar devem ser controlados pelo Indicador de Restrição, se aplicado, que deverá ser observado diariamente com o motor na rotação máxima de trabalho.
- Nos motores equipados com tanque de boia e filtro separador d’água, o dreno d’água e sedimentos também deverá ser efetuado.
Serviços de manutenção periódica preconizados pelo fabricante:
- Substituição do filtro de ar
- Substituição do filtro de combustível
- Substituição do óleo e filtro de óleo lubrificante do motor
- Verificação do sistema de arrefecimento
Ficou com alguma dúvida? Entre em contato com a nossa equipe!
Aproveite para conhecer as linhas de manuais automotivos do Simplo!